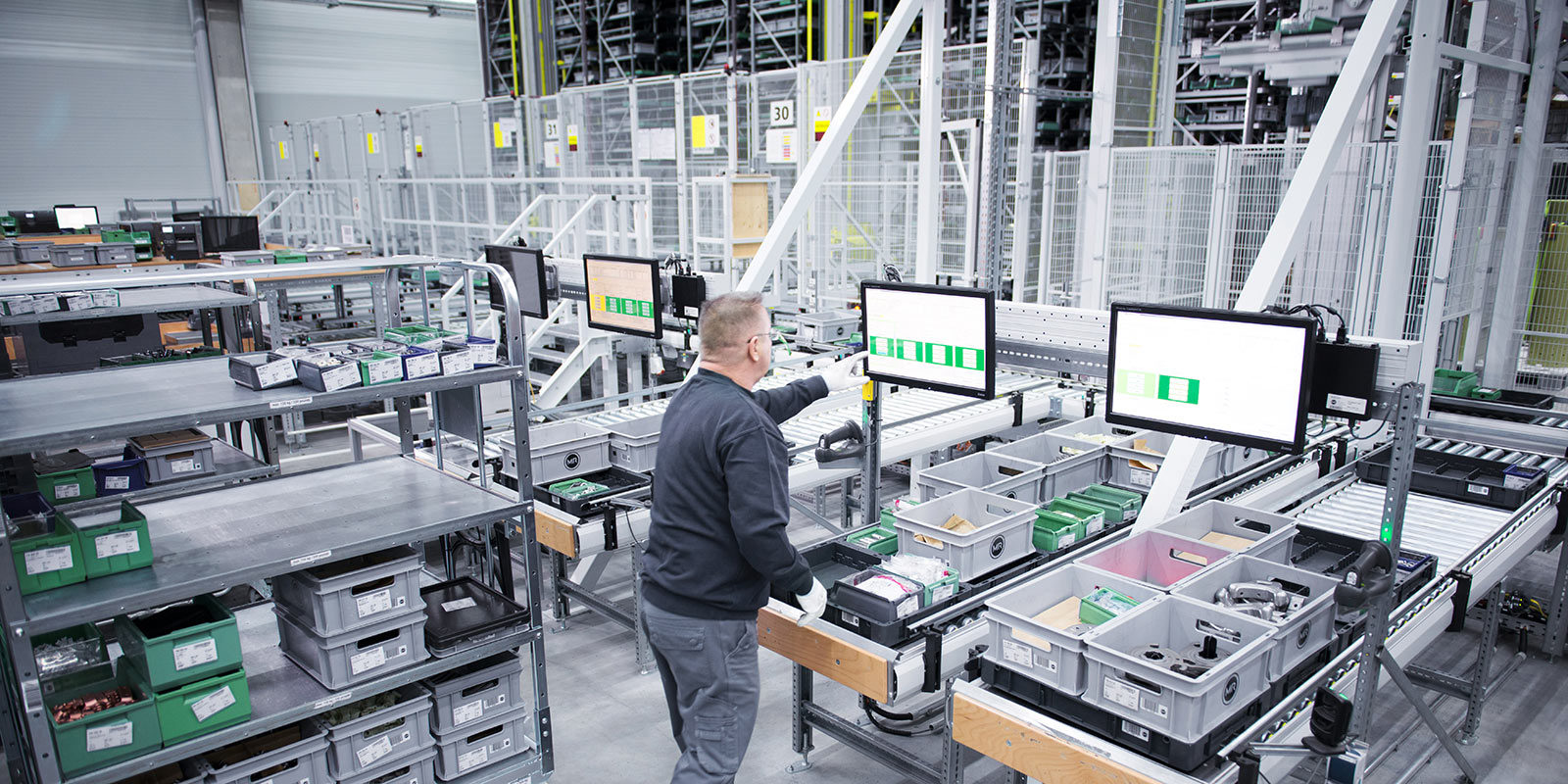
Maschinenfabrik Reinhausen
High performance intralogistics for production
Maschinenfabrik Reinhausen, headquartered in Regensburg, is with 3,300 employees the world market leader in the regulation of power transformers. Over 50 % of global electricity flows through MR products. In addition, the company offers turnkey solutions for the interaction-free operation of critical industrial applications and for the supply security in distribution networks. Testing and measuring technology for high-voltage devices and composite hollow insulators are also part of the product portfolio.
Customer:
Maschinenfabrik Reinhausen
93059 Regensburg | Germany
System:
4 sprinter AS/RS stacker cranes,
46.000 bins and trays,
4 order picking stations,
5 maxloader AS/RS pallet stacker cranes,
8.700 pallets and bins,
4 order picking stations,
selektron WMS,
fork lift control system,
interface to SAP
Design criteria
MR’s decision to establish a new high-performance Materials Management Center (MMC) was determined by several reasons: the available space and warehouse capacities in both plants in the Regensburg area were no longer sufficient, and there was no option for any expansions either. Warehousing was distributed to nine company-owned facilities, plus two external locations, on a total surface of about 15,000 square meters. Besides the partly obsolete storage technology, there was a large number of interfaces involved, as well as a low degree of IT support and automation. All this made an efficient production supply impossible.
The solution
The new Materials Management Center (MMC) of Maschinenfabrik Reinhausen provides a maximum degree of transparency and availability for a precise production supply. With three warehouse systems, multi order picking stations, supply trains loaded according to withdrawal sequence, and an intelligent Warehouse Management System (WMS) including an innovative fork lift control system, the MMC organizes the needs-oriented and timely supply of production. Thus, MR fulfills a delivery reliability of 99.3 percent.
The three warehouse systems are the core of the new intralogistics. They are installed next to each other in the MMC building (100 m long, 76 m wide and 26 m high), making optimal use of space. The high bay warehouse (five aisles) has 8,700 storage locations for euro pallets (1,200 x 800 mm) and pallet cages. Furthermore, a large number of half-pallets is stored double-deep in this warehouse as well. The automated small parts warehouse (four aisles) offers 46,000 locations for bins and trays, which can be stored double-deep, too. The warehouse for large items (four aisles), which has been established between the automated small parts warehouse and the high bay warehouse, is operated by a reach truck. It can take oversize pallets and pallet cages in up to 2,000 storage locations. This warehouse area, too, is organized by the WMS psb selektron.
When picking the material, which has automatically been ordered by the production department, the operators are guided through the WMS psb selektron on large and clear screens at the workstations. In the staging area, ten tugger trains take over the material and provide all areas of production and assembly. The fork lift control system by psb also serves as control system for the supply trains and is integrated in the selektron WMS.
With the new MMC, implemented by psb, a number of strategic goals could be achieved: enhanced competitiveness, higher quality standards, reduction of stock and costs and higher availability. Furthermore, the warehouse floor space was reduced by 50 % with the new warehouse concept.
You can download the detailed project description on this page..