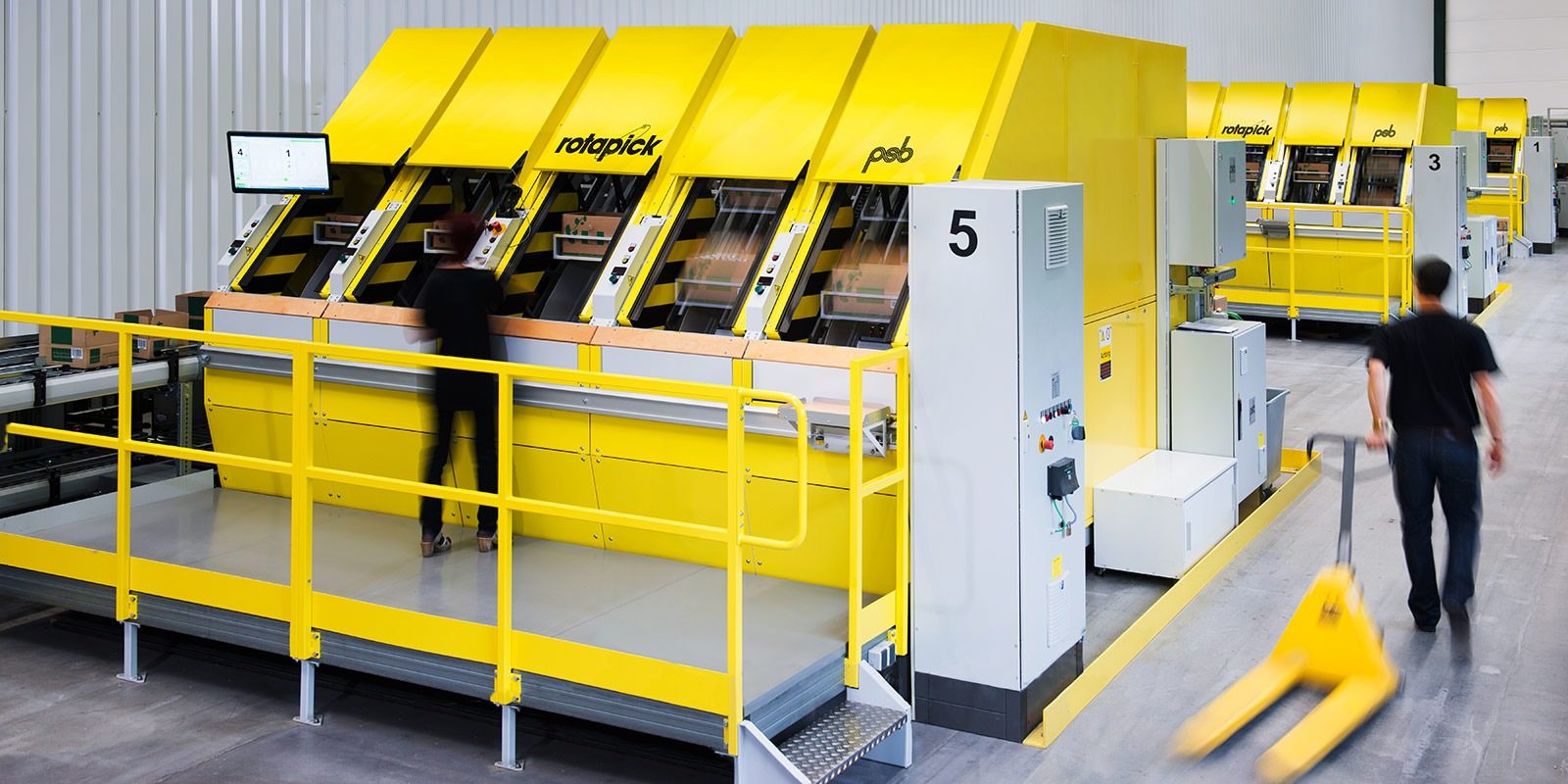
Order picking systems for every task
psb’s order picking systems impress with their economic efficiency and ergonomics. Different systems are available to suit the respective task: from manual order picking carts to fully automated high-performance workstations. We adapt the respective order picking facilities and systems individually to the requirements of your project.
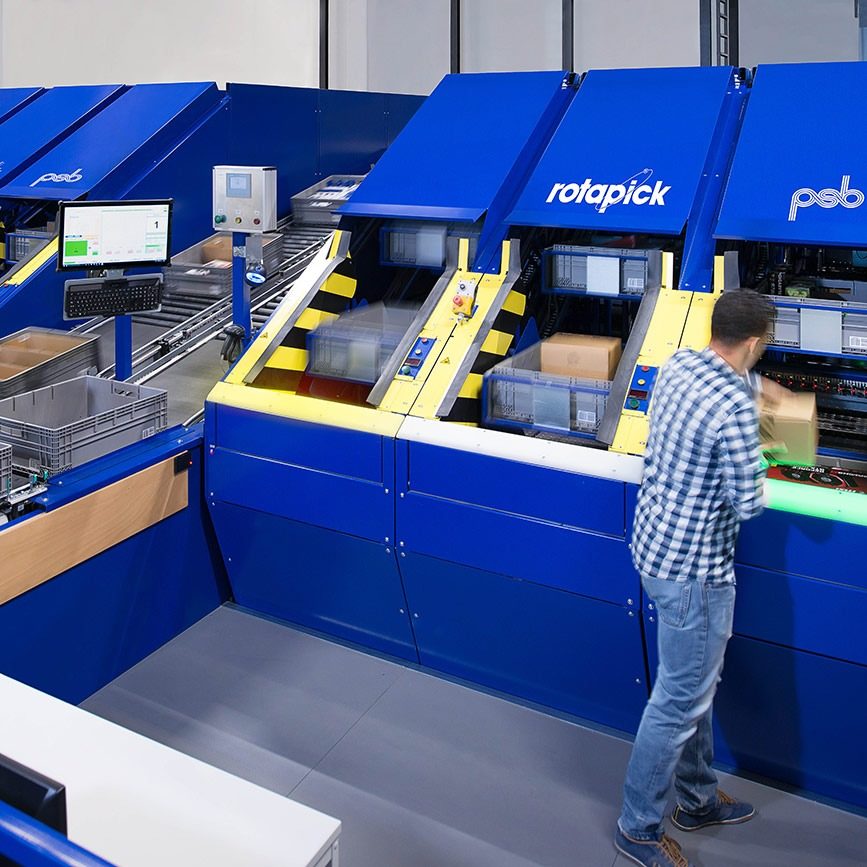
High-performance order picking system rotapick
Multi-source picking – Multi-order picking – Multi-target picking
Depending on the expansion stage, the modular psb high-performance system is able to buffer over 50 source or order totes at the picking station and, if necessary, make them available for picking within seconds. This eliminates uneconomical multiple transport from the warehouse to the picking station, which in turn significantly reduces order processing times. Another advantage is the order-based sequencing of goods.
With the rotapick, picking rates of more than 1,000 picks/hour can be achieved per workstation.
In these Best Practices, you will find out more about the high-performance order picking system, rotapick, in use and its integration into the respective overall intralogistics system:
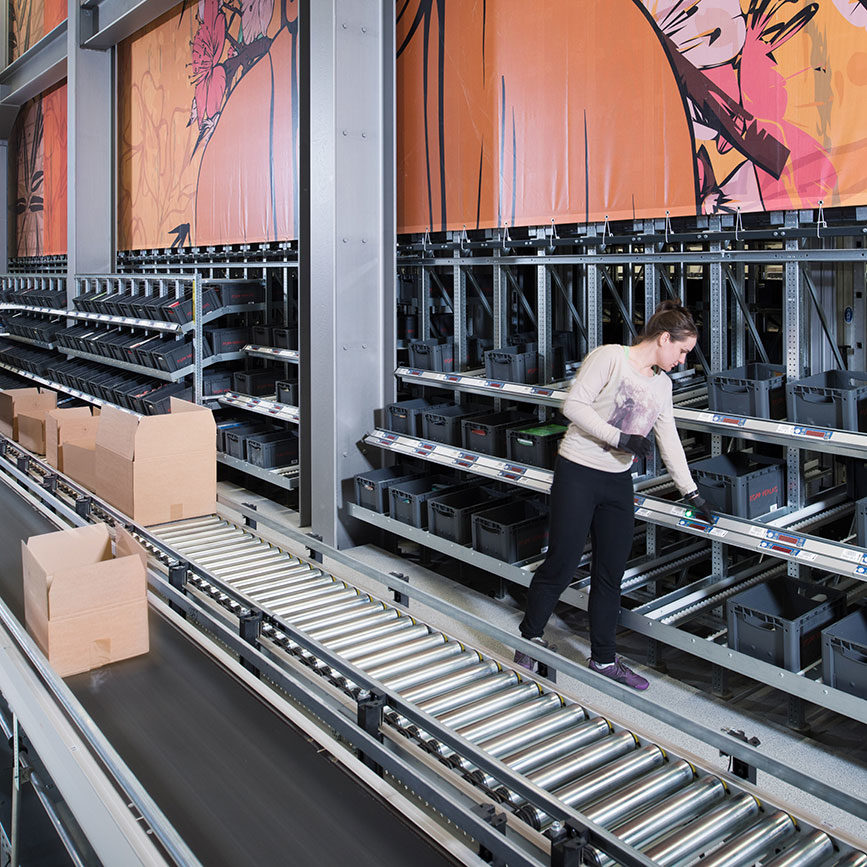
Flow rack – static or dynamic
At order picking workstations on the flow rack, product totes are permanently available for order picking in flow channels. By means of »pick by light« displays, the quantity to be taken from an article tote and added to the order tote is indicated to the employee.
In static flow channels, always the same article is provided, whereas in dynamic channels, product totes are exchanged by an AS/RS stacker crane. Order picking with flow channels can be applied for all load-handling devices, from cartons to pallets.
Find out more about this picking system in these Best Practices:
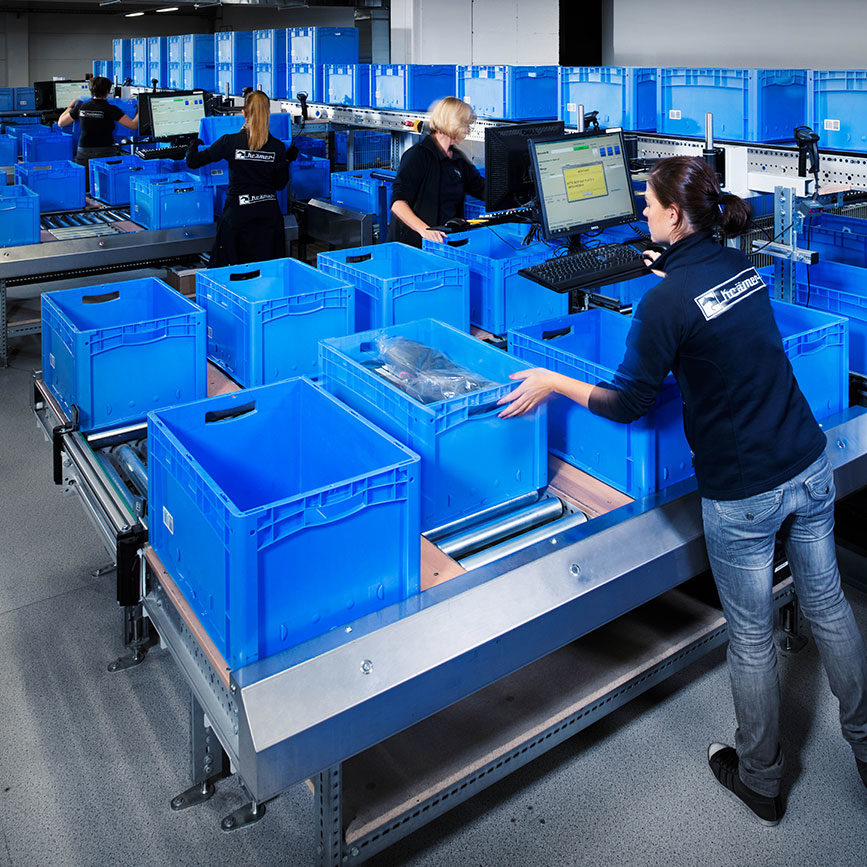
Multi-order picking station
The use of multi-order picking stations is useful if the majority of the orders contain identical parts or to relieve sequence-specific outsourcing.
Several order totes are available to the employee at the same time. The »put to light« display indicates to the employee in which order tote the respective picked quantity of goods is to be placed.
Find out more about this picking system in these Best Practices:
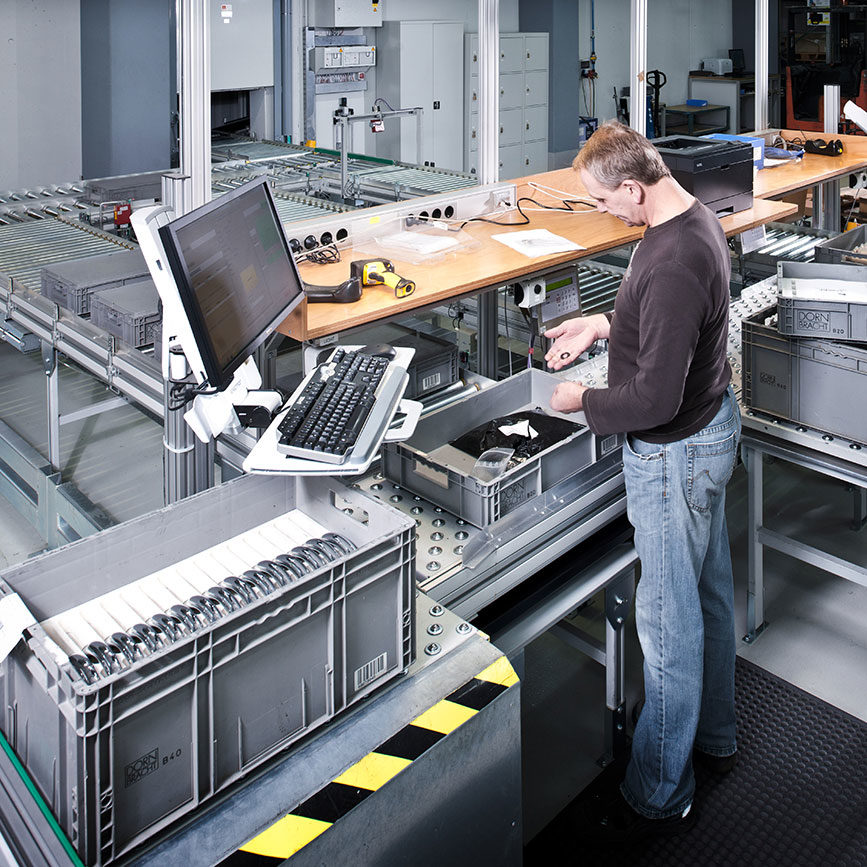
»One-to-one« picking
At the picking workstation »goods to person with one-to-one picking« just one order tote is available to the employee.
Product totes are made available from the warehouse in the correct sequence via conveyor technology. When the order is completed, the order tote is sent for dispatch and the next order begins.
Find out more about this picking system in these Best Practices:
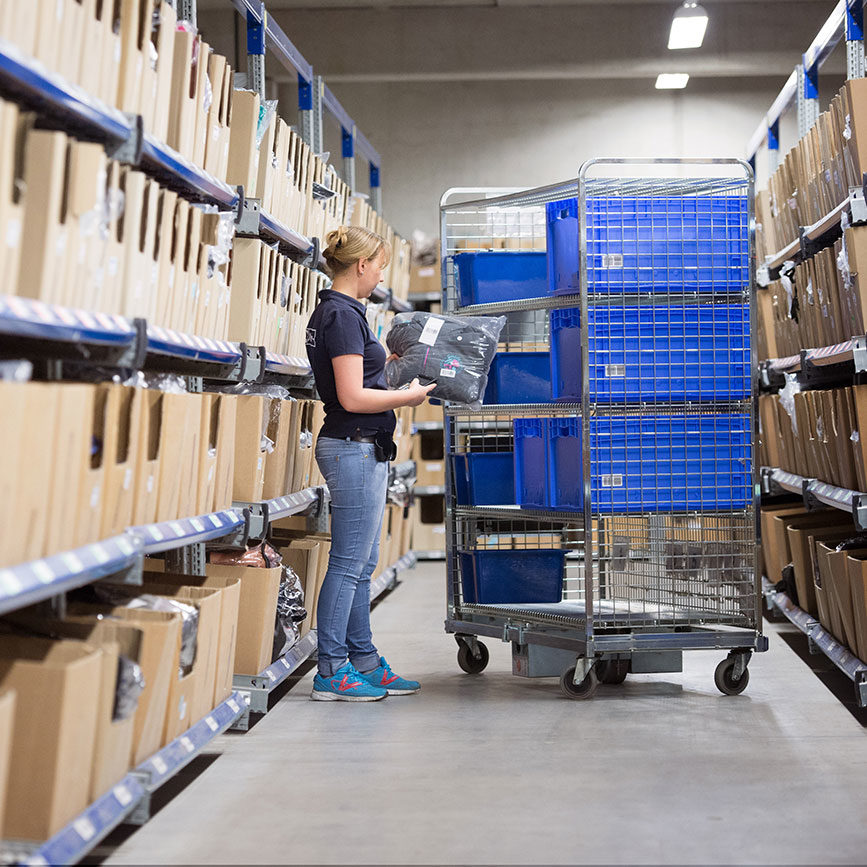
Manually operated order picking carts
Picking with manually operated picking carts in warehouse aisles is recommended, for example, for a large number of »A« items or for bulky goods.
Depending on the solution, different aids such as »pick by voice« or »put to light« are used.
Find out more about this picking system in these Best Practices: