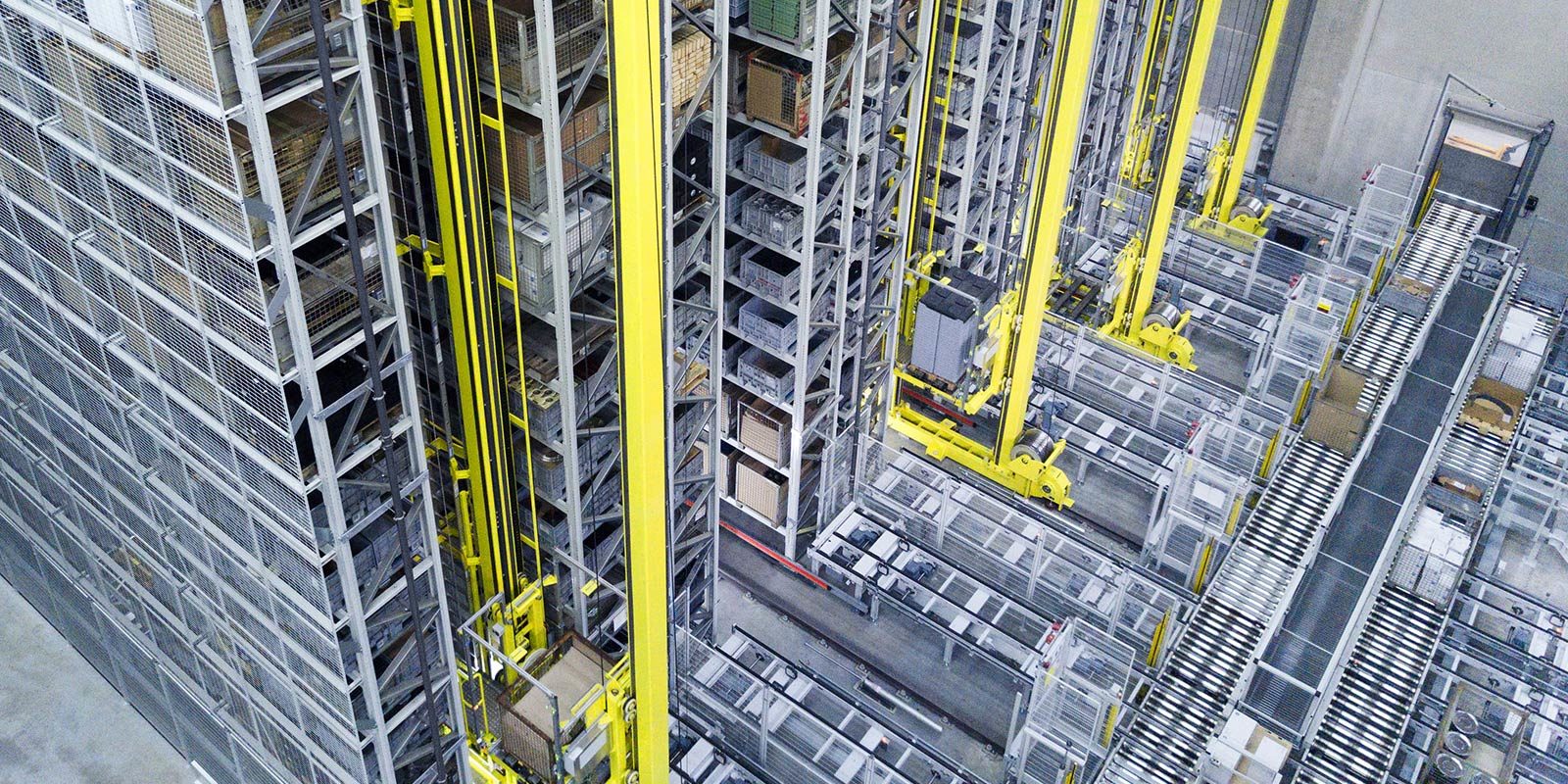
Individual intralogistics solutions from psb for heavy-load carriers
For heavy-load carriers – pallets, crates, totes, trays – we offer a wide, coordinated system portfolio: from transport to storage to order picking.
This also makes it possible to handle heavy or large parts automatically in production and distribution processes.
In addition to systems for large storage units, we also have combined solutions with which both pallets and half-pallets can be moved and stored.
Storage of heavy-load carriers
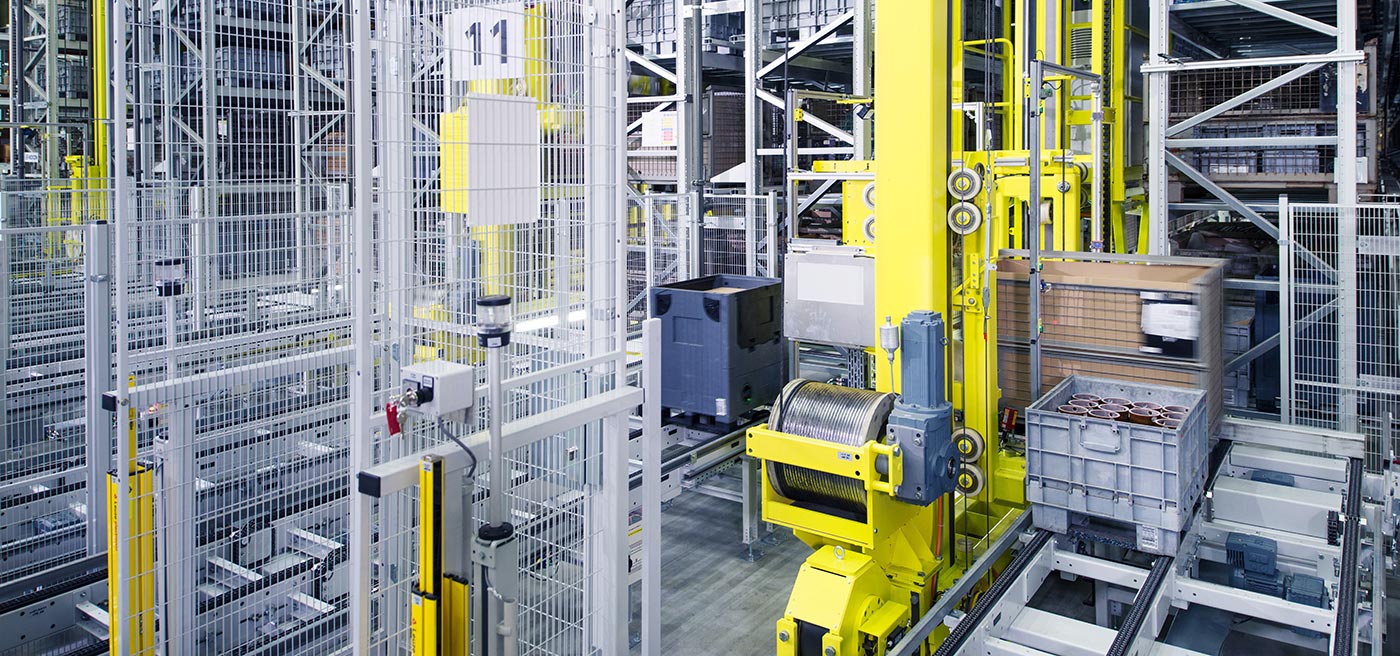
The maxloader AS/RS stacker crane from psb is suitable for storing heavy-load carriers such as crates and pallets with loads of up to 1,250 kg. These automatic stacker cranes have a dynamic performance that sets standards in their class and enables double-deep storage of the load-carrying units.
Multi-deep channel warehouses with a very high storage density are what the psb pallet shuttle is used for. A pallet AS/RS stacker crane transports the shuttle to the assigned channel, from where the pallet is deposited by the shuttle at the specified location. The energy supply of the new pallet shuttle is provided by supercapacitors. In addition to an economical system layout, this enables a high degree of flexibility when using the system, for example, through the use of several shuttles per AS/RS stacker crane.
Transporting heavy-load carriers
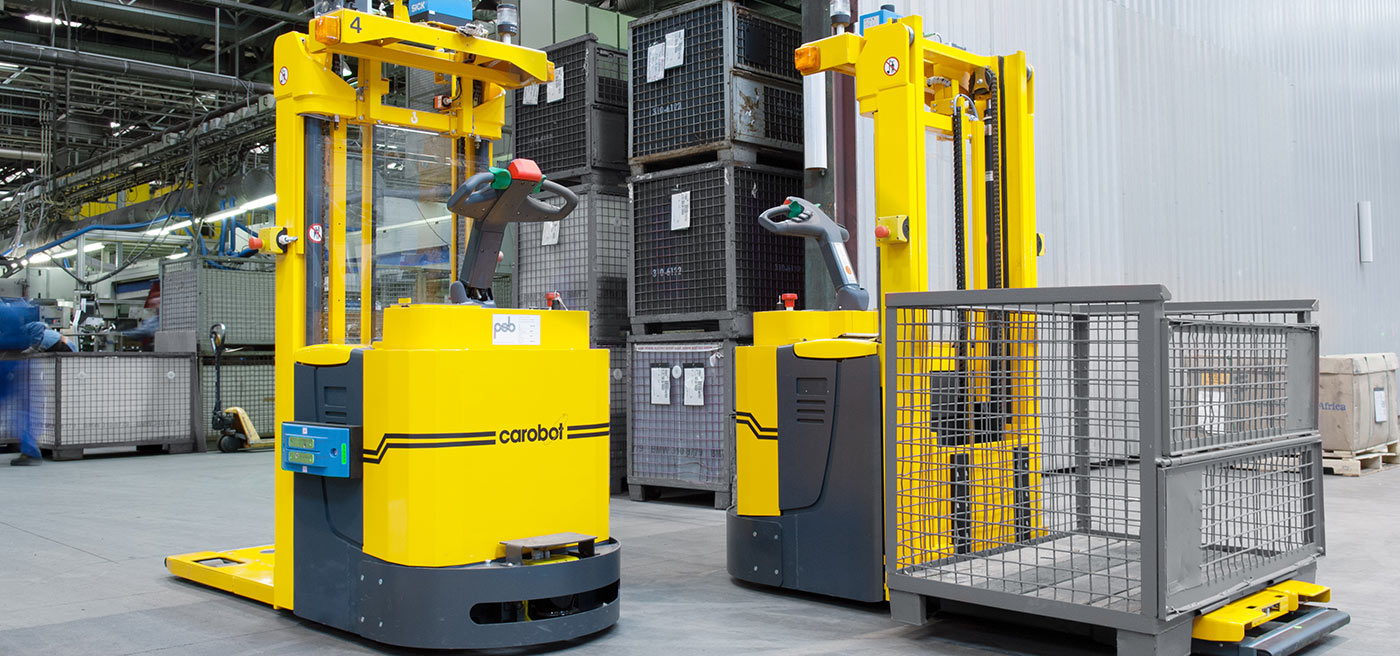
Heavy-load conveyor technology enables the horizontal and vertical transport of heavy-load carriers such as pallets and crates. Additional elements such as scales, shape controls or monitoring devices for pallet runners are used depending on the individual requirements.
Driverless transport systems (AGVs – Automated Guided Vehicles) are flexible links between the various company areas, such as between production and storage, or between incoming goods and the supply warehouse. The self-driving, battery-operated vehicles are suitable for a wide range of transport tasks. The maximum configuration of the modular system is the integration into an overall concept with selektron host computers for flexible production interlinking and dynamic solutions for distribution tasks. The vehicles are controlled by laser navigation. Preparatory work on the floors is no longer necessary.
Picking of heavy-load carriers
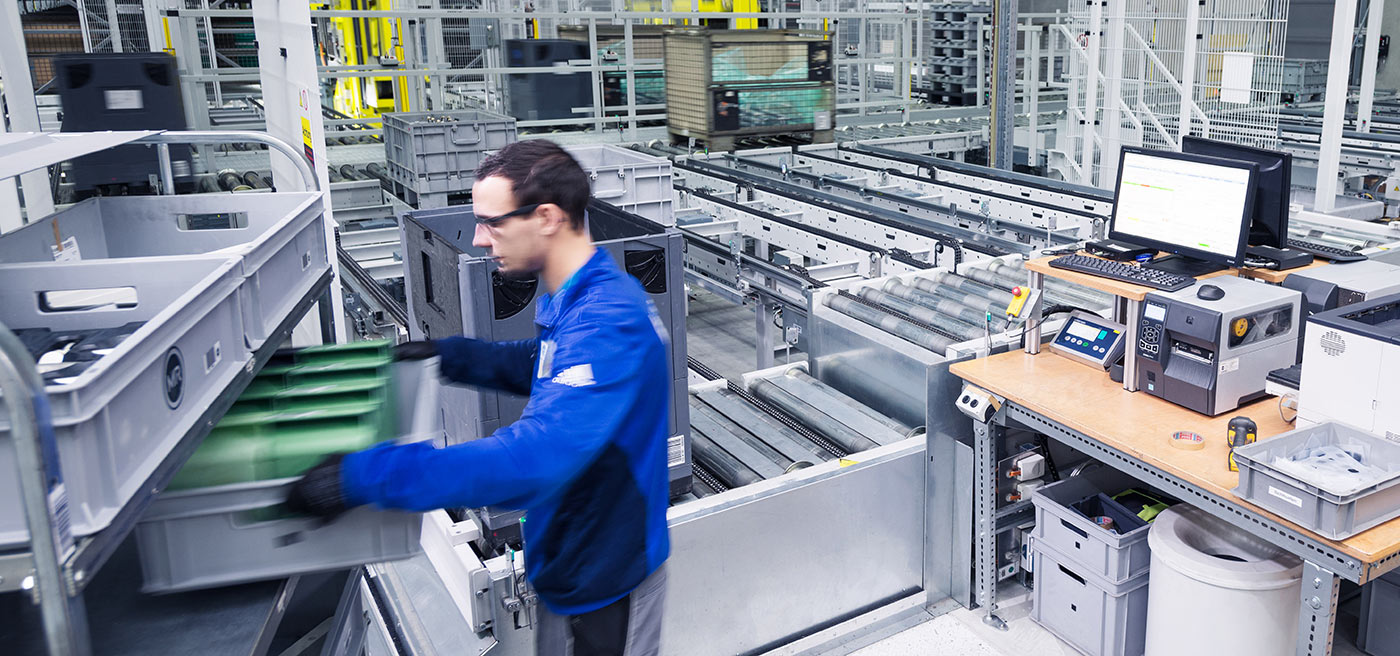
At the picking workstation “goods to person with one-to-one picking”, just one order tote is available to the employee. The heavy-load carriers are made available from the warehouse in the correct sequence using conveyor technology.
At order picking workstations on the flow rack, the pallets are permanently available for order picking in flow channels. By means of »pick by light« displays, the quantity to be taken from a pallet and added to the order tote is indicated to the employee.
Additional Functions
The solutions for these three main intralogistics tasks can be supplemented with special functions to complete your system: automatic stacking and unstacking by robots, automatic or manual loading systems for tugger trains, scales, lifting tables and many more can be integrated.

Best Practices
As we are thinking in terms of systems, we do not offer individual products, but complete intralogistics systems. This ensures that everything is intertwined and systems are able to run highly profitably for decades. Our intralogistics systems are tailor-made for your requirements and dimensioned to be future-proof when commissioned. Right from the start, we consider all eventualities and take into account many options for scalability and adaptation to changed business models.
Find out more about our coordinated intralogistics solutions for heavy-load carriers in these Best Practices: