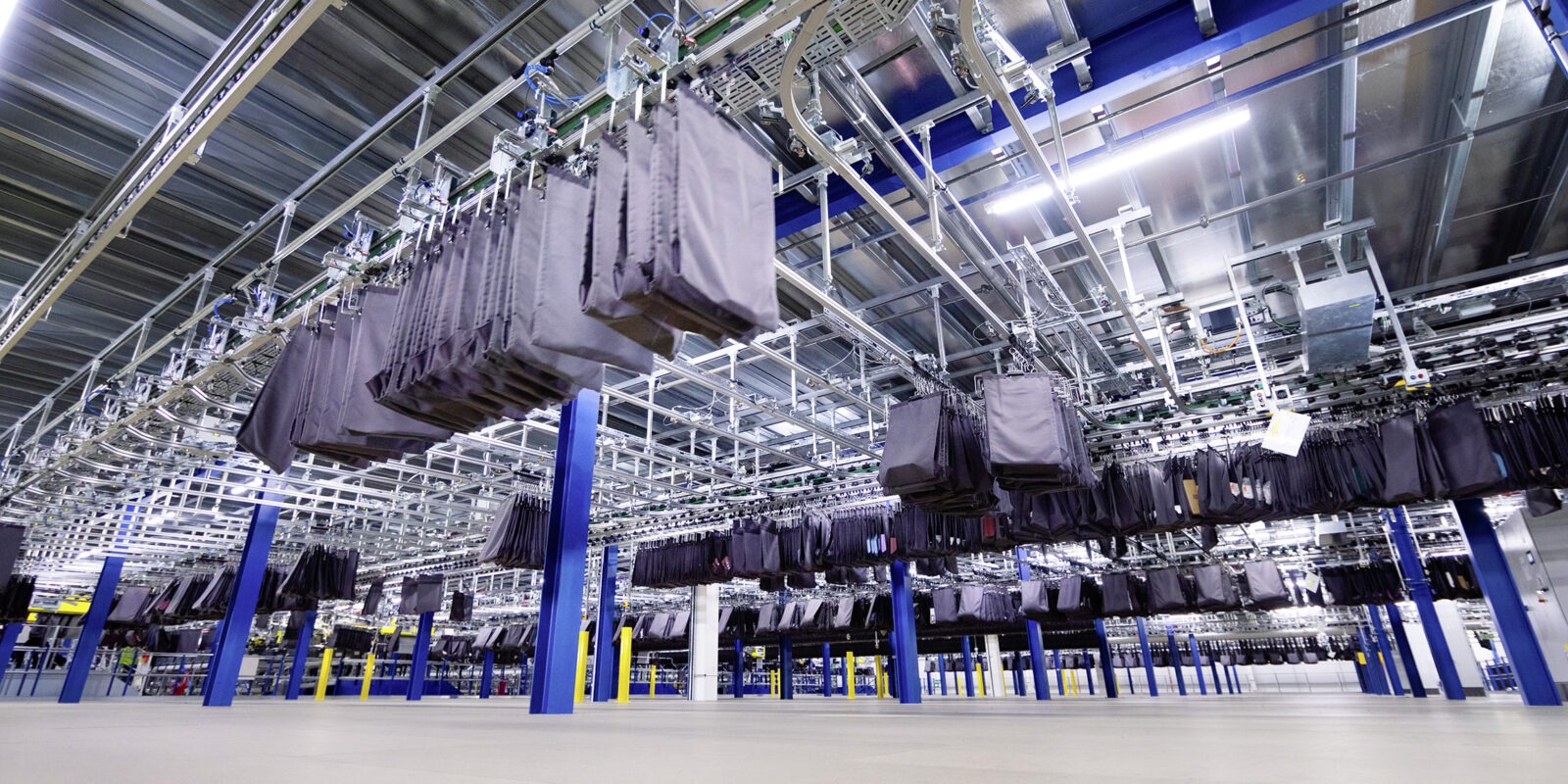
Boohoo
Efficient and flexible
Pouch sorter in fashion e-commerce
Boohoo.com is a dynamic British e-commerce retailer targeting young, value-oriented customers. Founded 2006 in Manchester, the company has grown enormously with a portfolio of brands, including market leading original brands and reputable high street brands acquired through acquisition.
Customer:
Boohoo.com UK Ltd,
Burnley | United Kingdom
System:
5 pouch sorter modules, each with 6 pouch loading stations and 18 packing stations, Tote buffer for single-piece orders (SINGLES) and orders with more than one item (MULTIS), 26 SINGLES packing stations, 10 tote stackers, Cross belt sorter for shipping bags, 2 telescopic boom conveyors for fully automatic trailer loading
Design criteria
Due to Boohoo’s rapid growth, the distribution centre in Burnley was expanded to a total area of approximately 17,000 m². In the course of this expansion, two additional halls were built, each with a five-storey mezzanine construction and a connection to the four existing halls. The additional space is primarily used to store clothing and accessories in cartons.
The previously existing logistics processes, from goods receipt to despatch, were handled manually. In order to manage the increasing throughput figures and to optimise the internal processes, psb intralogistics implemented an automated intralogistics solution with a largescale pouch sorter as the core system.
The solution
With the new system solution, the individual customer orders are combined in batches, which means that items for many different orders are picked together. The individual parts are picked manually in the storage areas of the various buildings. With the so-called »pickwalks«, a distinction is made between multi-pack orders and single-item orders. A sophisticated conveyor system transports the picked totes from the different storage areas or buildings to the sorting area. There, the first step is that they are consolidated in a tote buffer until items from the batch have been picked.
Single-piece orders are routed directly to dedicated packing workstations and prepared for despatch. The orders with more than one item are initially sorted to order by a downstream pouch sorter with 13,500 pouches. This means that the goods, which have been collected in pick-optimised order, and which are unsorted in the collection totes, are then sorted into individual customer orders. All the goods of an order arrive together at one packing station, regardless of which storage area they come from. This solution ensures very fast and efficient management of the warehouse as well as organisation of the picking process.
The modular design of the pouch sorter with five independent sorting modules enables a sorting capacity of up to 30,000 individual parts per hour. The particular advantage of the installed solution is the flexibility of the system: depending on the time of day or season, the sorting modules can be switched on separately and the performance of the system can be adapted to the required throughput.
Via eight inducts, the downstream despatch sorter is loaded with shipping bags coming from the different packing areas. The shipping bags, which vary greatly in size, are sorted to 100 end points. Two of these end points are each connected to a telescopic boom conveyor, that enables fully automatic trailer loading. The system achieves a sorting capacity of over 12,000 shipping bags per hour thanks to the sophisticated arrangement of inducts at the end points.