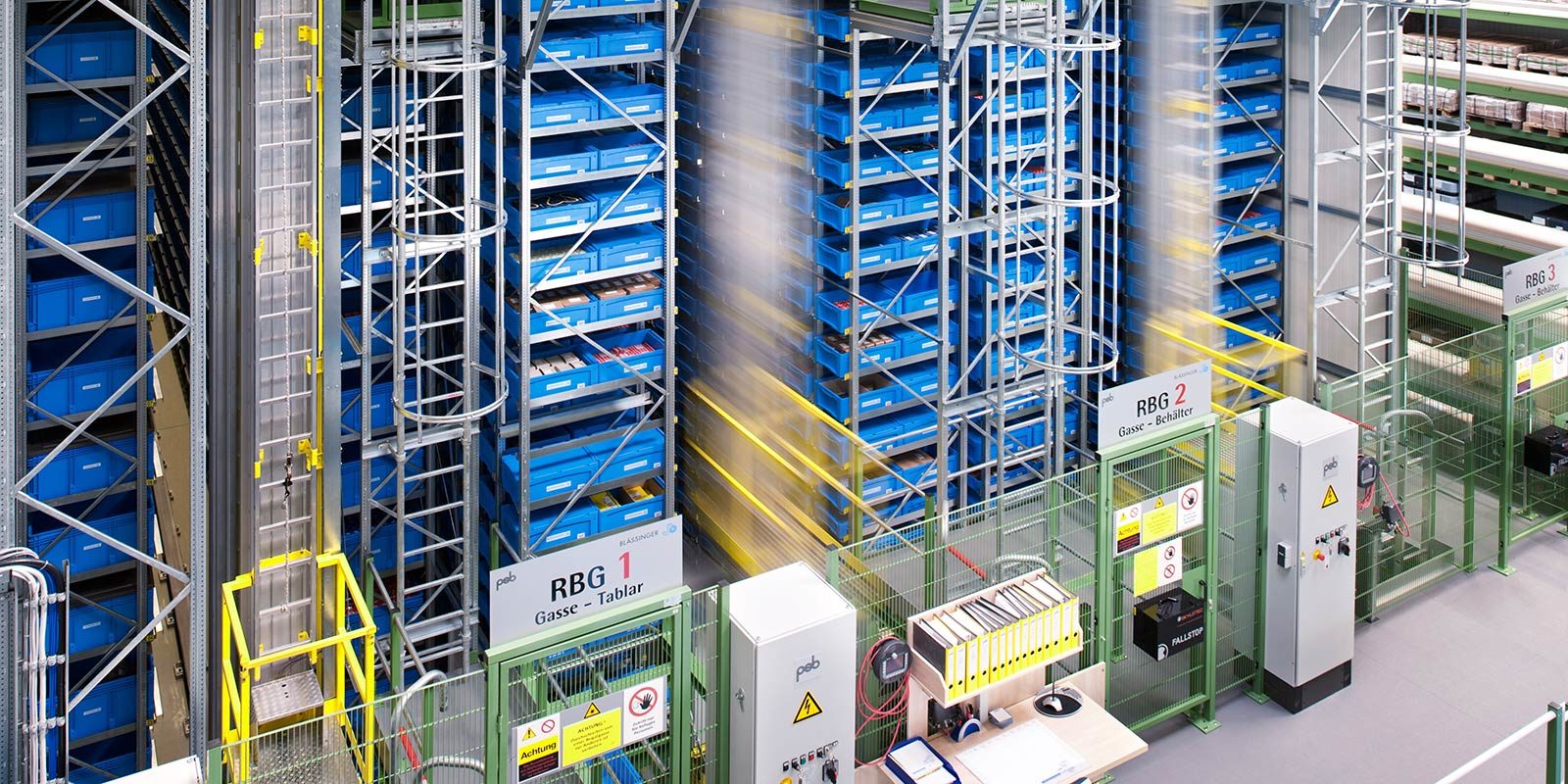
Josef Blässinger
Automated order picking and replenishment
warehouse for roller bearing distributors
Driving, steering and moving; that is what Josef Blässinger GmbH + Co. KG has been doing since the company was founded in the year 1930. Customer service, flexibility and quality are always its highest priorities.
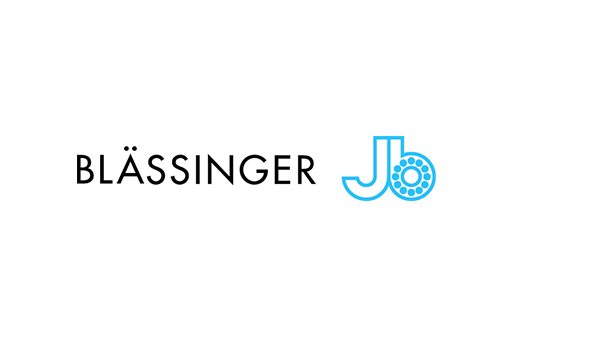
Customer:
Josef Blässinger GmbH + Co. KG,
73760 Ostfildern | Germany
Systems:
4 goods-receiving, bin and tray conveyor system, small parts warehouse with 2 sprinter and 1 runloader AS/RS miniload systems, order picking stations, 4 packing stations, selektron WMS, SCADA Win CC
Design criteria
In a time, when product cycles keep getting shorter and price pressure keeps growing, the optimization of business processes is the key to success »We’ve always been in motion and will stay that way« – this is the highest principle of Blässinger. In order to maintain this standard, also in the future, an automated order picking and replenishment warehouse was built at the company’s manufacturing location in Ostfildern (near Stuttgart).
The solution
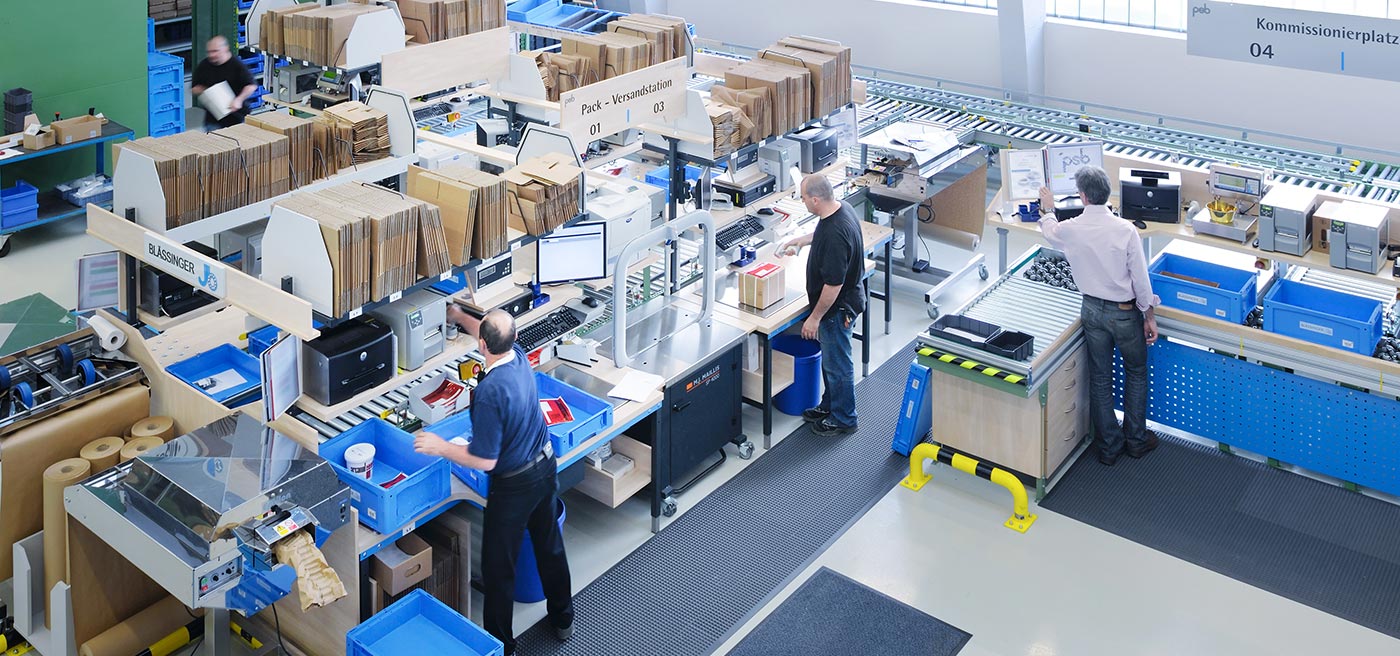
The tray and bin warehouse allows for the efficient storage and picking of high-quality roller bearings, linear engineering and drive technology products. The tray warehouse (one aisle) is operated by a runloader AS/RS stacker crane with »pull handling device technique«. A combined workstation, for goods-receiving and picking of large quantities and items, is directly connected with the warehouse; the trays are handled utilizing a twin-track conveyor system.
The bin warehouse (two aisles) is operated by sprinter AS/RS miniload cranes. It is connected by a conveyor system with three goods-receiving, four order picking and four packing stations. The bins are provided, in and out, with a psb roller conveyor system. The entire conveyor technology is operated without the help of pneumatic elements. The psb selektron WMS was supplied as a Windows-2003-Cluster-Server. The connection to the customer’s ERP system is realized via a network connection.