Crossbelt sorter
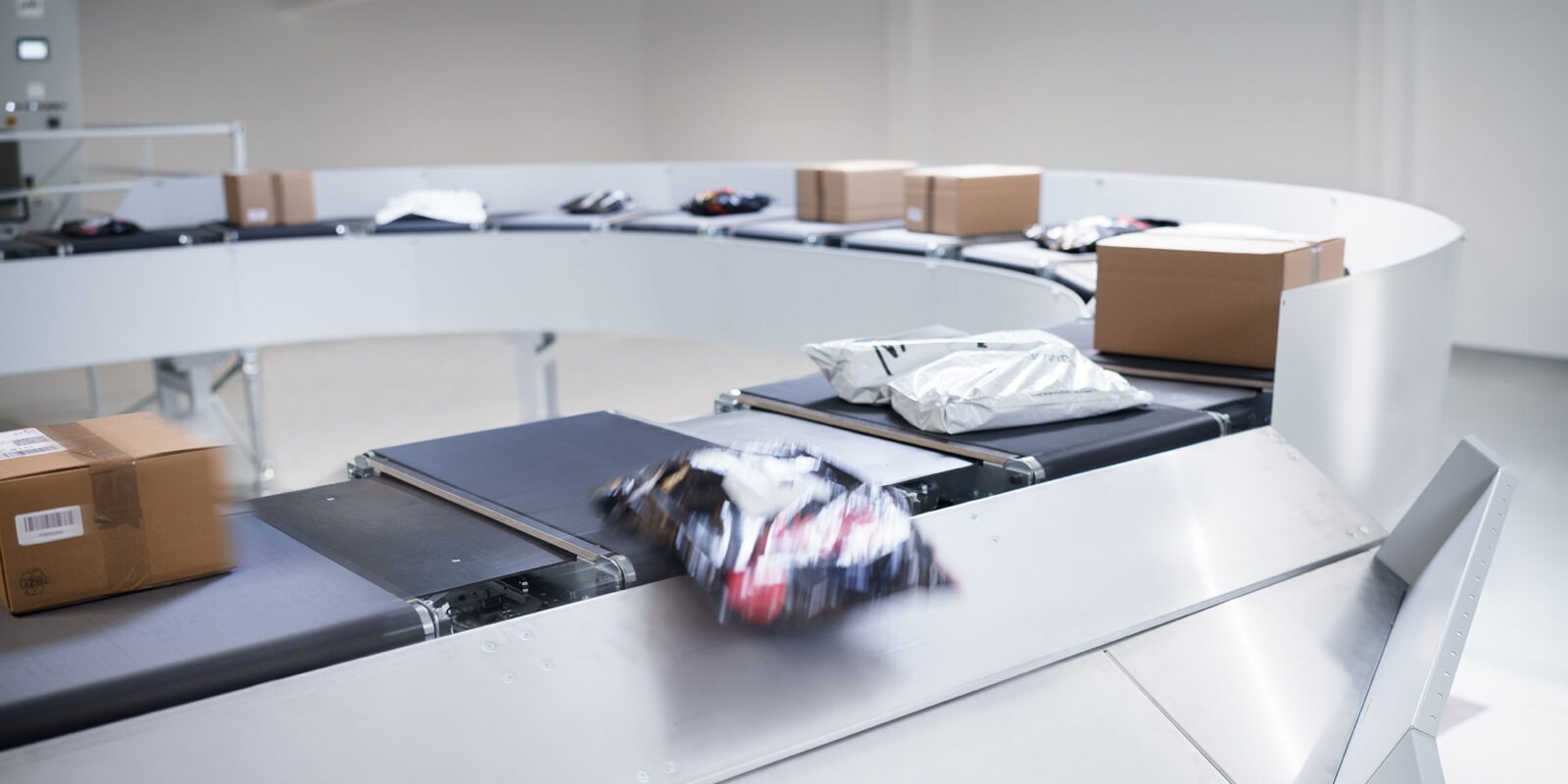
Automated high performance sorting system for flat pack goods
The psb crossbelt sorter is designed to transport and sort a mixture of different types of flat pack goods: totes, cardboard boxes, parcels and shipping bag. The three-dimensional sorting system can be flexibly customised to meet specific requirements.
Goods with dimensions ranging from 100 x 100 mm to 800 x 600 mm and a maximum weight of 35 kgs can be transported and sorted with a performance of up to 12 000 articles in an hour. With a specific version of the sorter, goods weighing up to 50 kgs can be handled as well.
Sorted safely and efficiently
The psb sorter with its flexible, three-dimensional layout with curved sections, ascending and descending sections, as well as the variable arrangement of infeed lines, outfeed and sorting sections is the ideal solution for a wide range of applications.
Thanks to the modular design of the sorter, the trolleys can be individually configured with dynamically driven crossbelts, from medium to maximum sorting performance. The items are automatically transferred via an infeed line onto the crossbelts of the runner blocks. Depending on the customer requirements, the items can be fed manually or via partially) automated infeed stations.
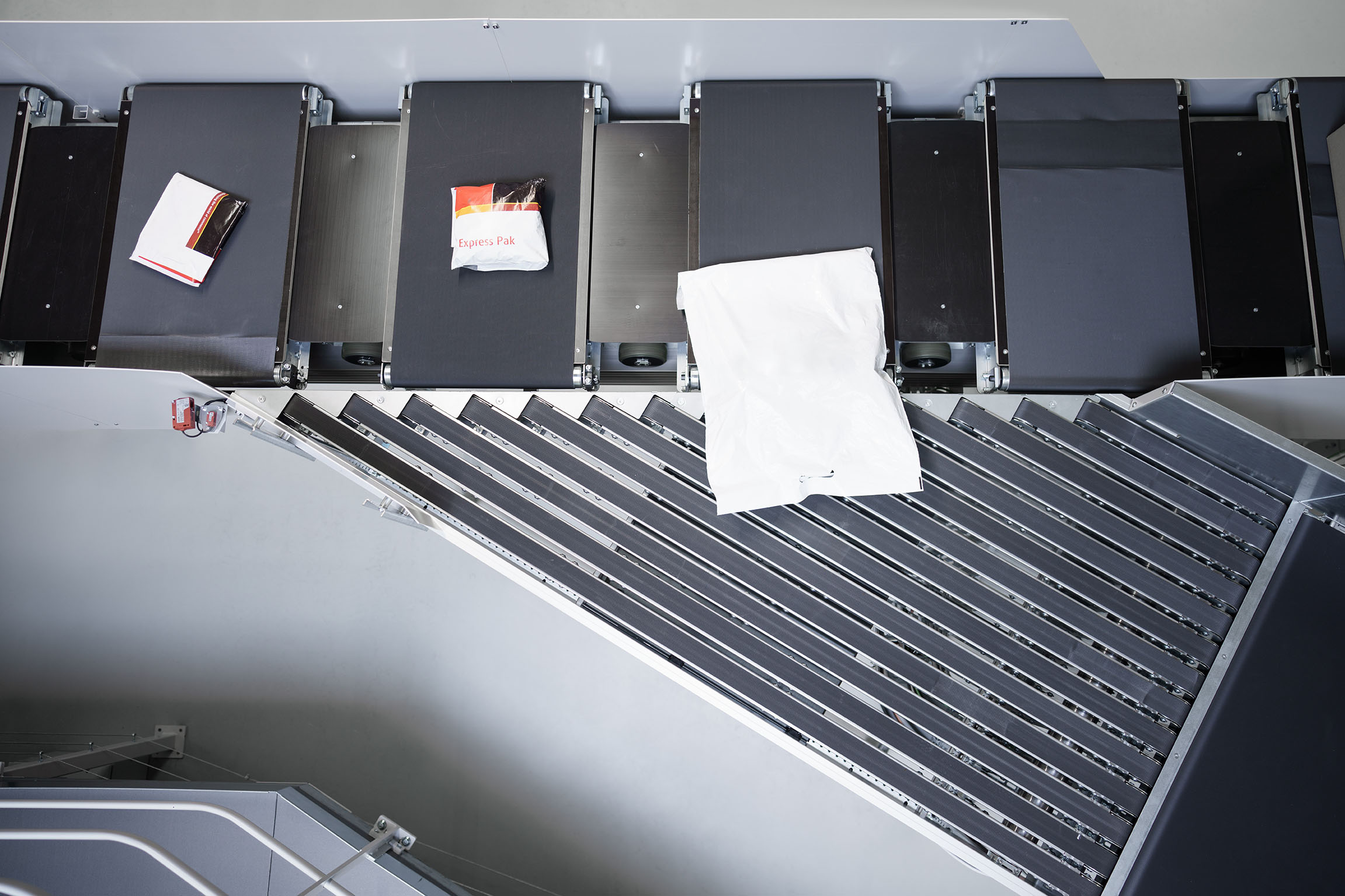
Intelligently controlled by psb selektron
The high performance sorting system is controlled by the psb selektron intralogistics software. The runner blocks are coded and »married« to an article after it has been taken over. This ensures permanent identification of the articles and constant monitoring of the position of the runner blocks and the position of the articles on a runner block.
Unique feature of the crossbelt sorter: Based on the recorded article parameters, the goods are transported and sorted carefully, by taking into account the individual type and properties. This means that different items, such as cardboard boxes and polybags, can be sorted in mixed operation with repeatable and reliable handling.
A combined use for different applications, such as retail and e-commerce, can be implemented, as can transfers to conveyor systems for the onward transport to other work areas.
The intelligent energy management is another outstanding aspect of the low-maintenance psb solution: special feature is the contact-less and therefore wear-free energy transfer to the runner blocks for driving the belts when taking over/discharging the goods.
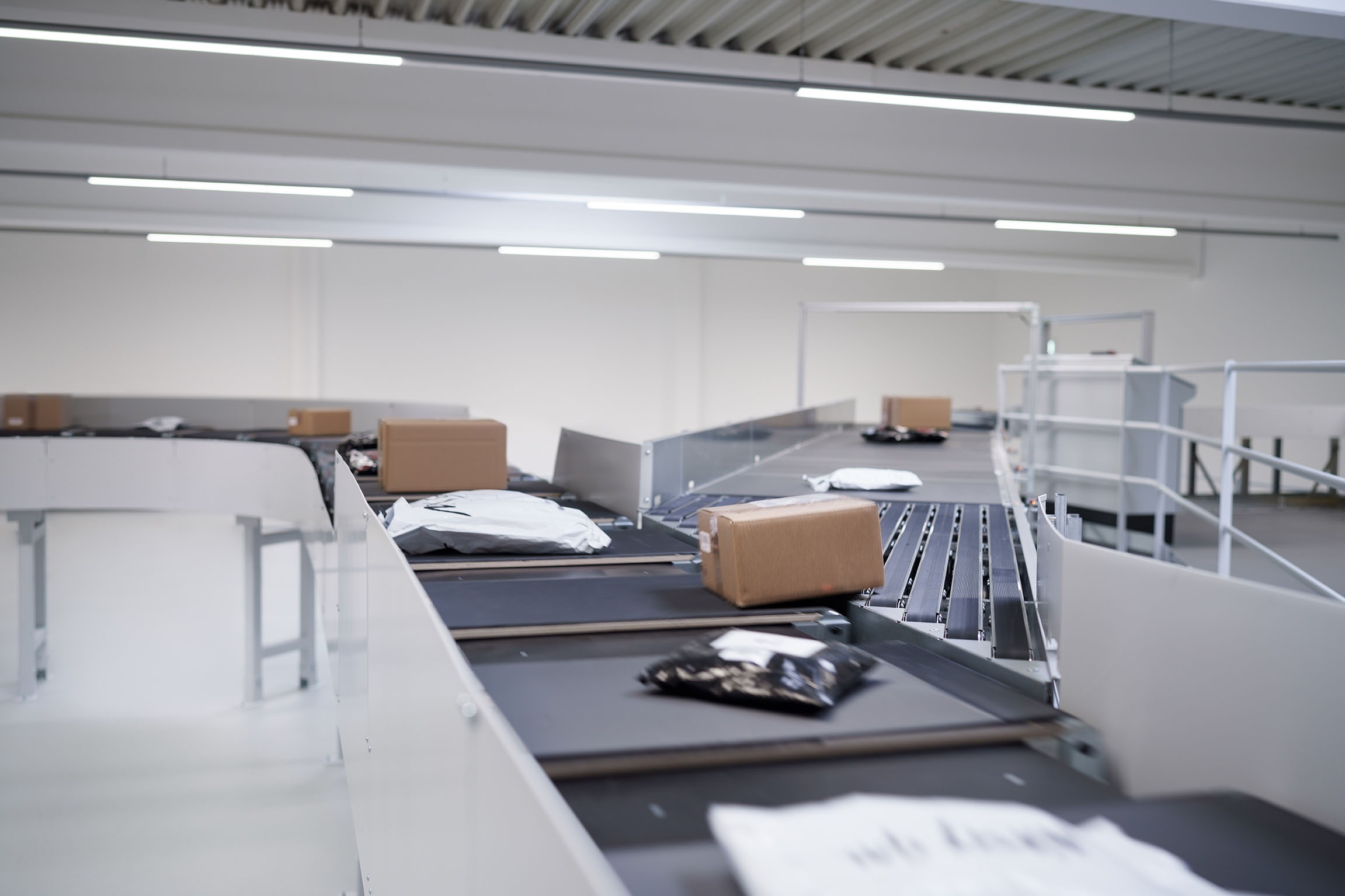
You might also be interested in
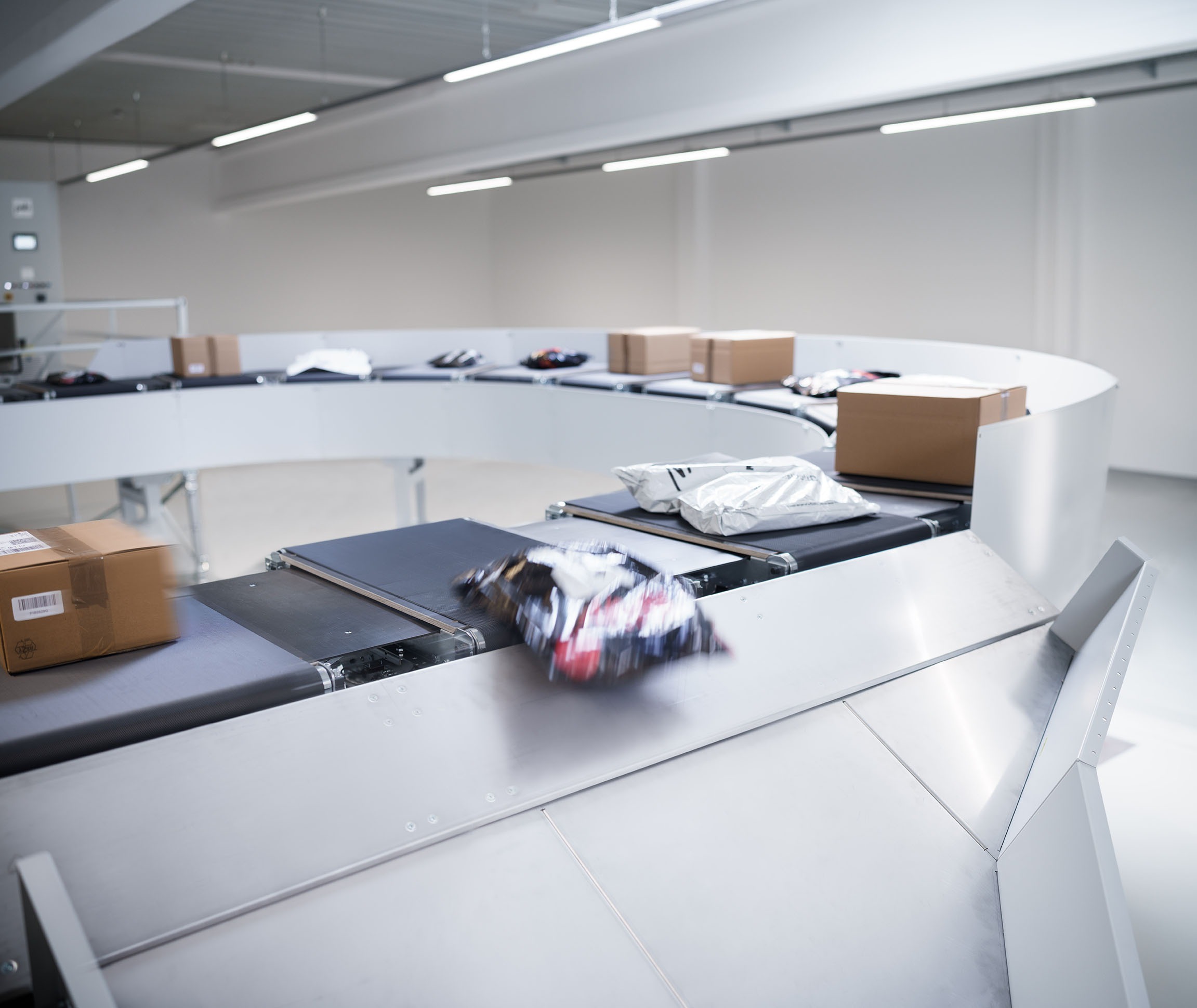
Sorting systems from psb intralogistics
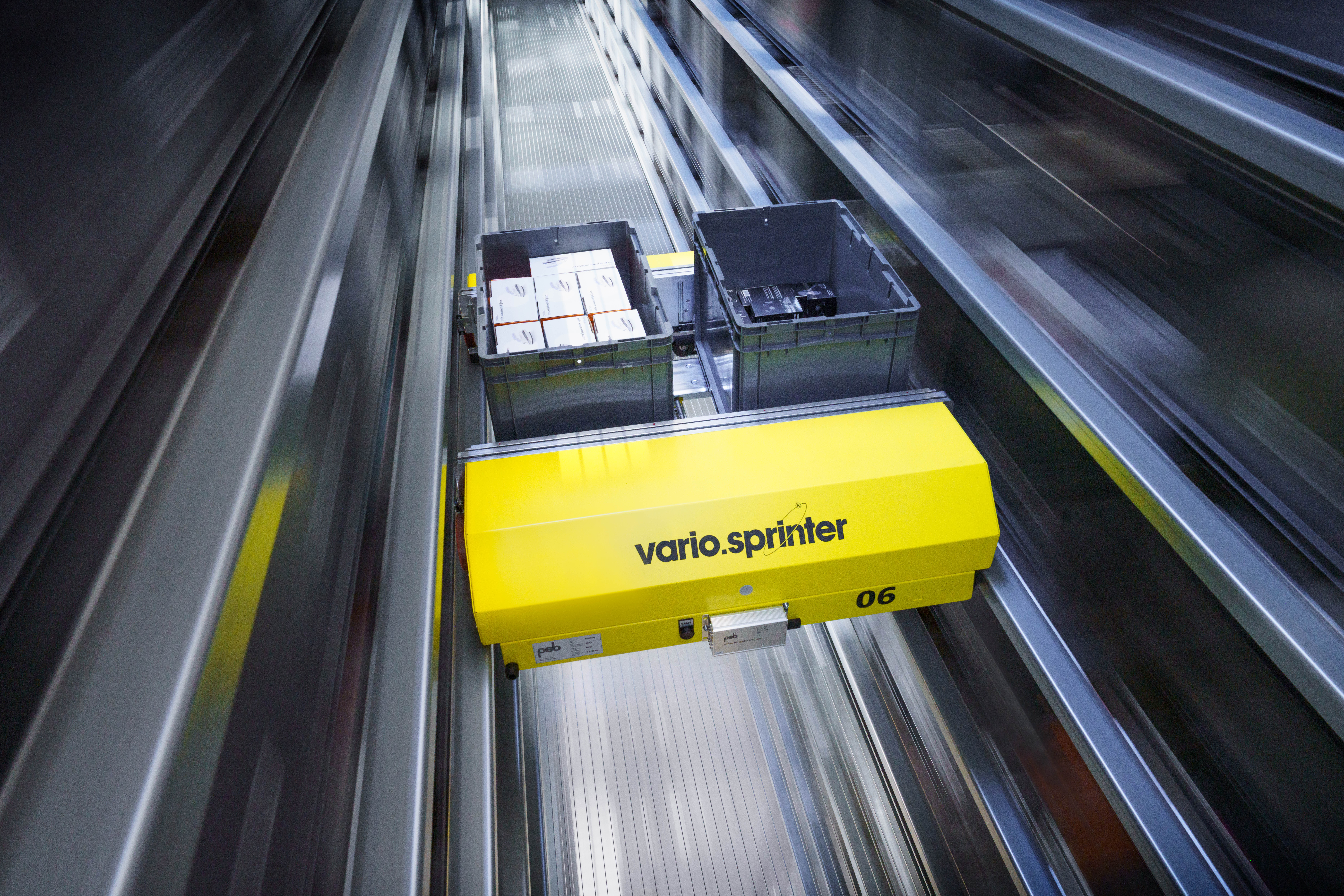